With shearing mostly wrapped up now (only rear half of Felix remaining), I’ve shifted gears to getting some of the fleece harvest washed!
I’m pleased to report that after a rocky start a few years back, Daphne’s wool is kind of coming into its own now. I’d have to dig back through the blog archives, because I’m otherwise kind of bad about keeping notes, but it seems like she’s hit her stride, fleece-wise. Lovely curly tips, med-long staple, nice soft handle, good “floof” factor. Think I’m going to enjoy playing with this batch!
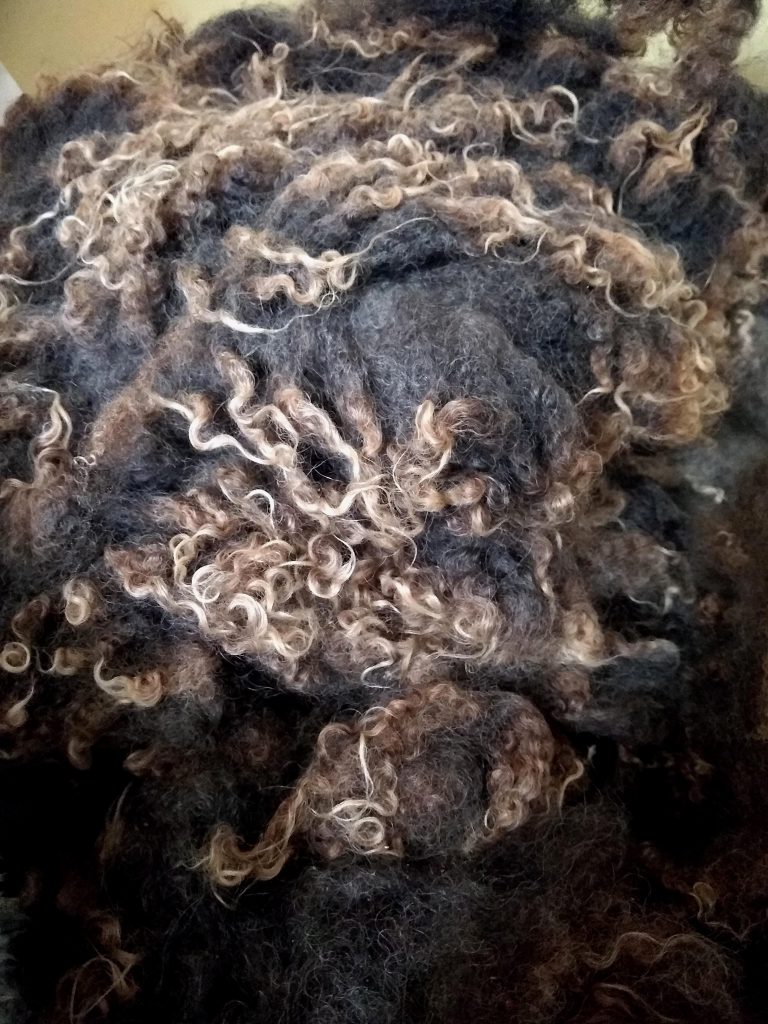
Felix’s wool is really interesting in how it’s changed over the years. Back when he was a youngun’, his wool was quite long and fine- but wavy rather than crimpy. Then there were the in-between years when both he and Frank were so felted that I couldn’t do much with their wool except make toupees for sock monkeys. But now, in his golden years, Felix is growing much finer & crimpier, albeit shorter, fleece. It’s always been harder to get washed because his lanolin is much more persistent than some others. So this year I decided to use my dye kettle setup with the propane burner to get the water nice and hot. I think it worked out ok.
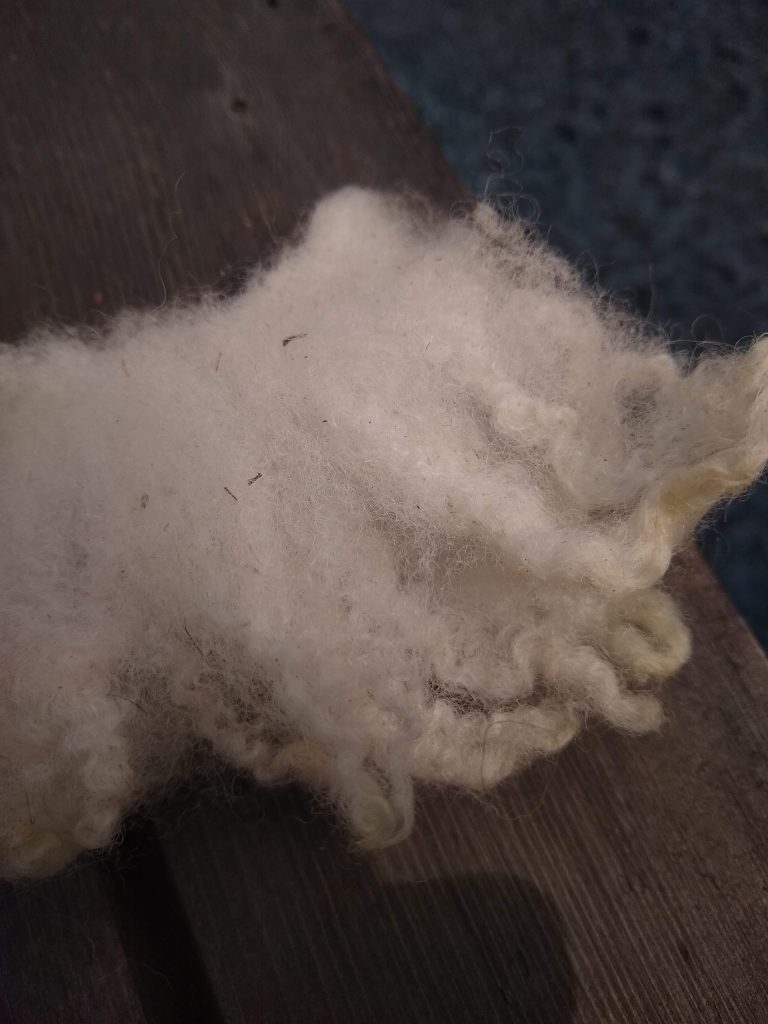
His wool is perfect for hand carding into rolags and spinning into lightweight woolen-style yarns
I’ve still got a bit of a backlog on Esther wool from last year, so trying to get that cleared out and cleaned up as well before starting on this year’s fleece. Maybe one more kettle full to go after this batch
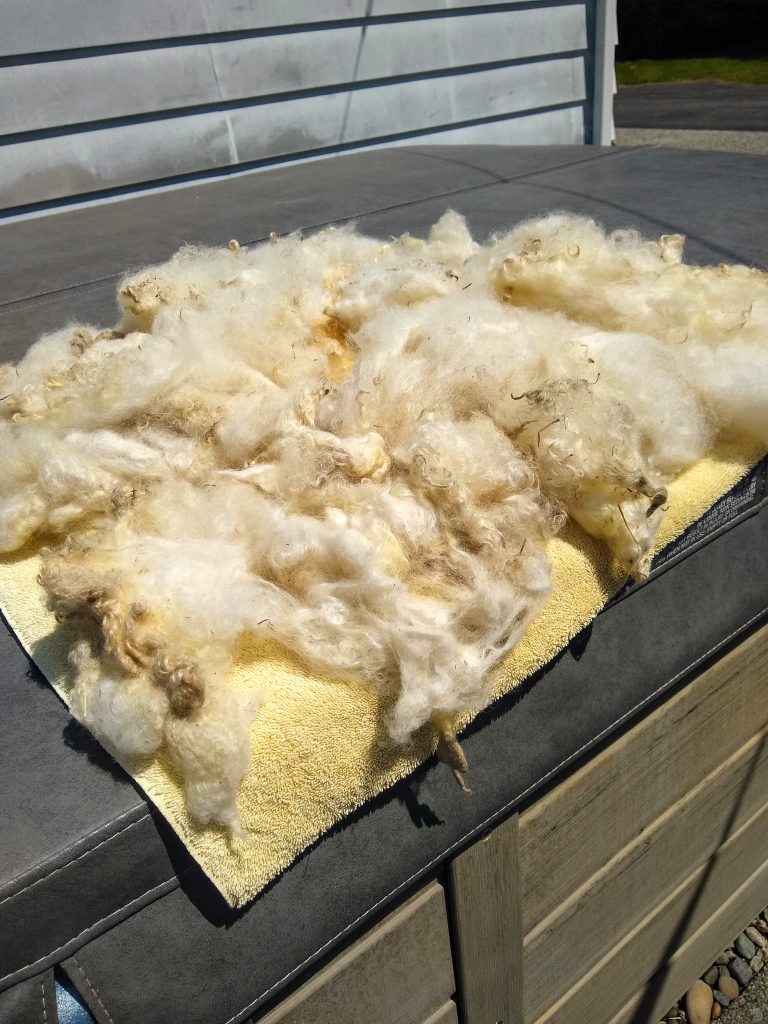
Washing Esther wool is always rewarding because of the complete transformation that it undergoes. From dirty, greasy, stinky to creamy white and glowing. These 2nds I’ll probably have to do some trimming of matting and yellowed tips, but it’s always work the work.
Haven’t started Dottie’s new fleeced yet, but she’s always an pretty easy washer.
And speaking of Dottie- her current sweater project is really coming along-
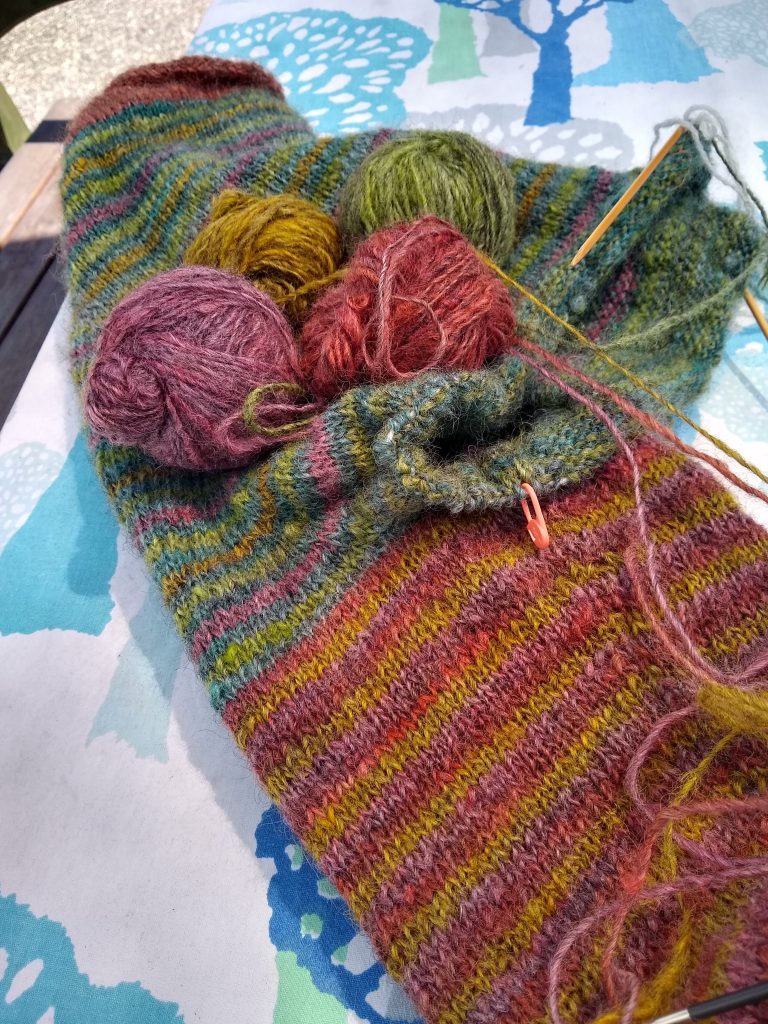
That’s a sleeve there in the foreground. I tried it on a little earlier today and am excited about how it’s shaping up. Feels really nice- light but cozy. and all that fabulous color. So fun.